Movin’ On Up? The Low Ceiling of North American Elevator Standards
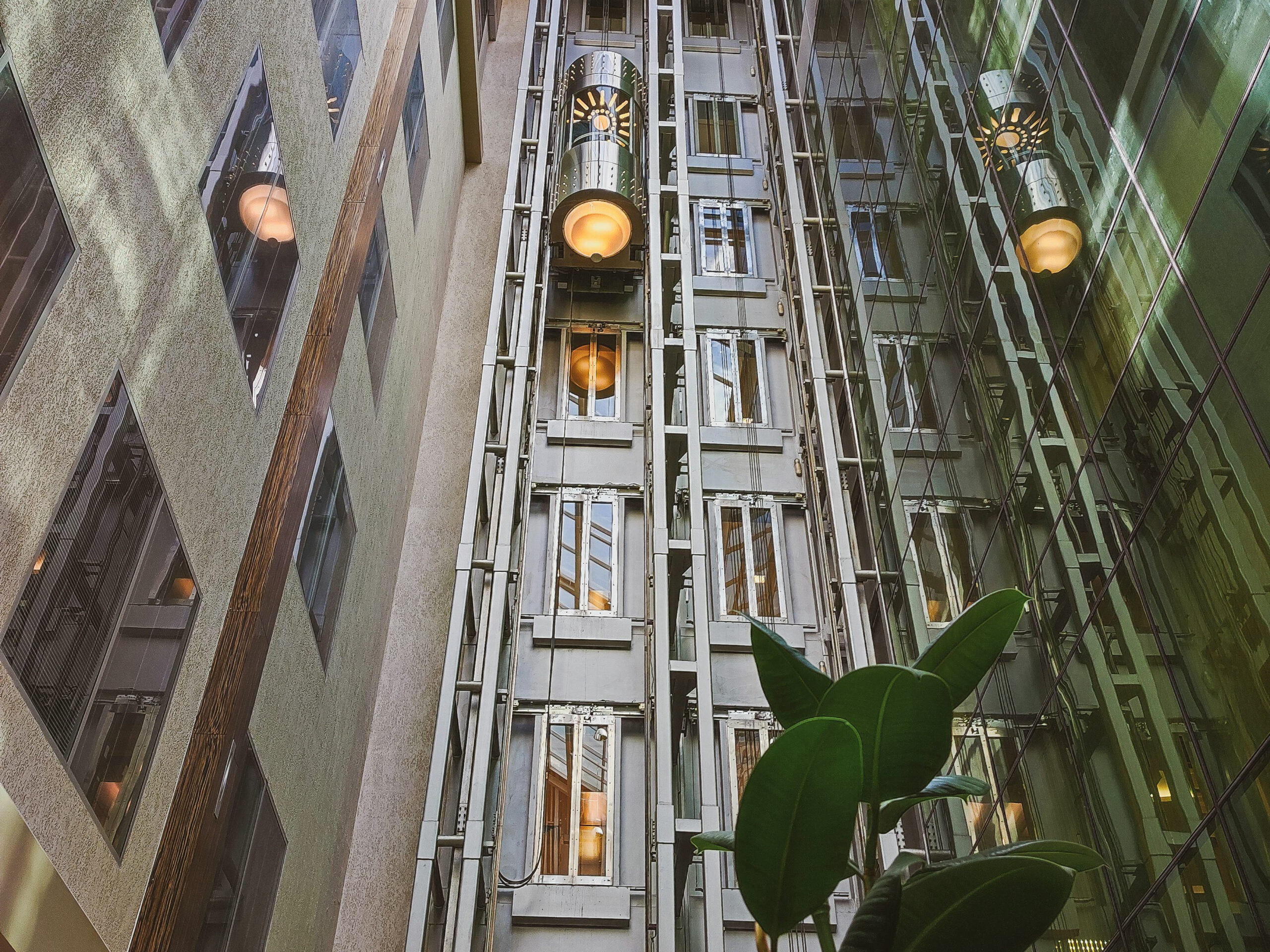
Why do we have so many walk-up apartment buildings without elevators in North America, and why are buildings with elevators so expensive compared to the rest of the world?
In a new report simply titled “Elevators”, Stephen Smith, from the Center for Building in North America, goes deep to document how our regulatory environment drives up costs—in the United States and Canada, elevators cost about three times as much as they do in peer countries—and reduces accessibility.
Smith identifies three key factors behind elevator cost bloat in the United States:
- Regulations requiring unusually large cabins that can accommodate a fully extended seven-foot stretcher, rather than a wheelchair and attendant
- A highly-specialized and insular market for elevator technician labor
- A patchwork of technical codes that do not align with the global standards
Compared to elevators in peer countries, elevators in the U.S. and Canada are unusually large. Unlike in Europe, where 3-foot, 6-inch by 4-foot, 6-inch elevators are common – big enough to accommodate a person in a wheelchair and an additional passenger – elevators in the U.S. and Canada must accommodate a 7-foot long stretcher with room to turn, as well as two attendants. The large size and weight capacity of these elevators makes them more expensive to install and maintain.
Perversely, these large elevators likely make the built environment less accessible than it would otherwise be. Wheelchair users seek out buildings with at least two elevators to avoid being trapped in their homes in the event that one goes out of service. American and Canadian elevator standards make these buildings less common for two reasons.
First, they encourage the construction of walk-up apartments with no elevators at all. These walk-up buildings rise to four, five, or even six stories—heights that would seem absurd in Europe, where most apartment buildings taller than two floors have at least a small elevator. Second, they incentivize developers to build as few elevators as possible, so a single elevator will serve 50 to 100 apartments and only very large buildings have multiple elevators. Again, this is in contrast to Europe, where 10 to 12 unit point access blocks often have a small elevator.
Smith also suggests that perverse labor incentives are part of the problem. His research shows that the elevator workers’ union for the United States and Canada, the International Union of Elevator Constructors (IUEC) appear to restrict the supply of skilled elevator installation, operation, and maintenance workers, using licensure to isolate markets and increase the barriers to entry for new practitioners.
Unlike in Europe, where tradespeople are trained in public schools, elevator workers in the U.S. and Canada learn the job through competitive, difficult-to-access apprenticeship programs that are run by the union; and new apprenticeships are restricted to ensure full employment of the existing workforce.
Similarly, where EU labor agreements allow Polish elevator technicians to work in Germany and France, American and Canadian workers cannot move between regions to find work because many states have onerous licensure requirements; for example, elevator mechanics working in Massachusetts must have completed a full three-year apprenticeship in Massachusetts.
Finally, IUEC agreements with elevator manufacturers forbid the use of labor-saving preassembly and prefabrication techniques that have reduced costs elsewhere in the world.
A Closed Market, Arbitrary Standards = Higher Costs
The U.S. and Canada’s elevator market is also largely separate from the global market thanks to a unique regulatory environment. In the late 1960s, the European Union set about creating a single technical standard for elevators that would apply throughout the continent, with the twin goals of maximizing safety and enabling free trade throughout the continent.
Since then, most of the world has adopted the European EN 81 elevator standards, allowing for a global market in parts for roughly ten million installed elevators around the world. The U.S., on the other hand, maintains its own A17.1 standard; and local jurisdictions around the continent generally adopt various versions of it to the one million elevators here, creating a disjointed patchwork of regulation even within The U.S. and Canada.
As a result, “there are vastly more parts available for countries following European rules than for the US and Canadian markets,” leading to higher prices and fewer elevators, with the accessibility effects noted above.
Further, many U.S. and Canadian regulations are not based on any actual data about building safety; and regulators routinely ignore the costs that new requirements impose on construction. For example, the 2006 code change that raised the minimum size of elevators to accommodate a seven-foot stretcher, rather than a six-foot, four-inch stretcher, was proposed by a fireman in Glendale, Arizona, who “was concerned that a sports arena being constructed would have elevators that would not accommodate… stretchers extended into a fully flat position.”
The cost impact was simply stated as ‘None.’ ‘Just think about if the patient was you,’ the proponent stated in his reason statement.”
Decreasing Accessibility in the Name of … Accessibility?
These well-intentioned regulations also ignore the tradeoffs in access they create: while larger elevator cabins make it easier to transport patients, the high costs the requirement imposes also increases the likelihood that buildings will not have any elevators at all, and that emergency responders will have to carry the patient down multiple flights of stairs. As Smith puts it: “small cost increases are each written off as individually negligible, and the negative accessibility, life safety, or other consequences of higher costs leading to fewer new elevators or new buildings generally are never considered.”
Smith concludes with a few straightforward policy recommendations: to bring down elevator costs, the United States should adopt nationwide standards, ideally in line with the European standards; allow smaller elevator cabins, especially in smaller buildings; and reform elevator technician training and licensure.